The municipal road (CM1062) is the main access to and from the small village and was cut to traffic due to erosion and partial collapse of the dam. Requalification of the Road-Dam by means of landfill consolidation using micropiles. A total of 126 piles were installed: 88 vertical and 38 inclined (25°) piles. These were all Ductile Iron Piles of 170/7,5mm, driven by wet method, and having a 270mm conical shoe. All iron material was supplied by Tirol Rohre GmbH (TRM). As per the designer requirement, one test pile and 4 reaction piles were also executed, using the same methodology.
The installation of the shaft-grouted piles requires pumping cement mortar (C25/30, with maximum grain size <4mm) that will fill up the inner and outer (annulus) space of the pile.
Challenges
A narrow working platform created difficulties in locating material and equipment. Positioning of the rig was even more challenging for the inclined (raked) piles. Besides the reduced area available, the production target was ambitious, associated to the urgency of reestablishing this access road.
Pile installation required the mobilization and lifting of 5m length ductile iron pipes. These were coupled to the hydraulic hammer and correct alignment had to be confirmed before and while driving. This operation was more demanding when having the 25° raked piles.
Concrete mix had to be correctly adjusted with the batching plant to have the adequate properties of pumpability and retardant, allowing for prolongated operation. Concrete availability and supply, associated to the far distance to the jobsite, have also created interruptions on the production cycles.
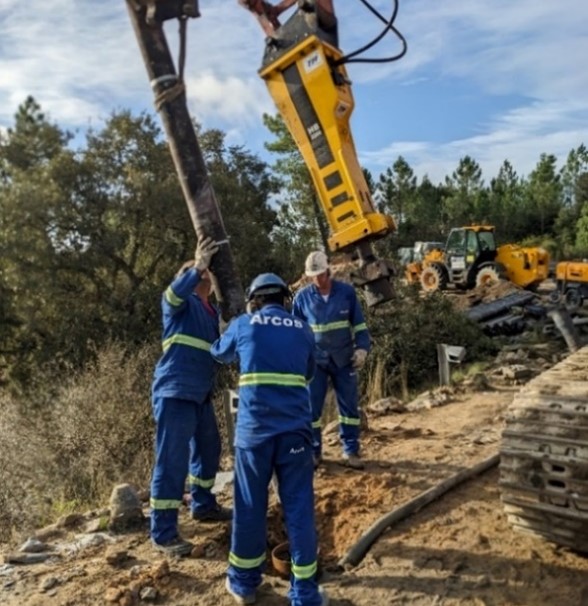
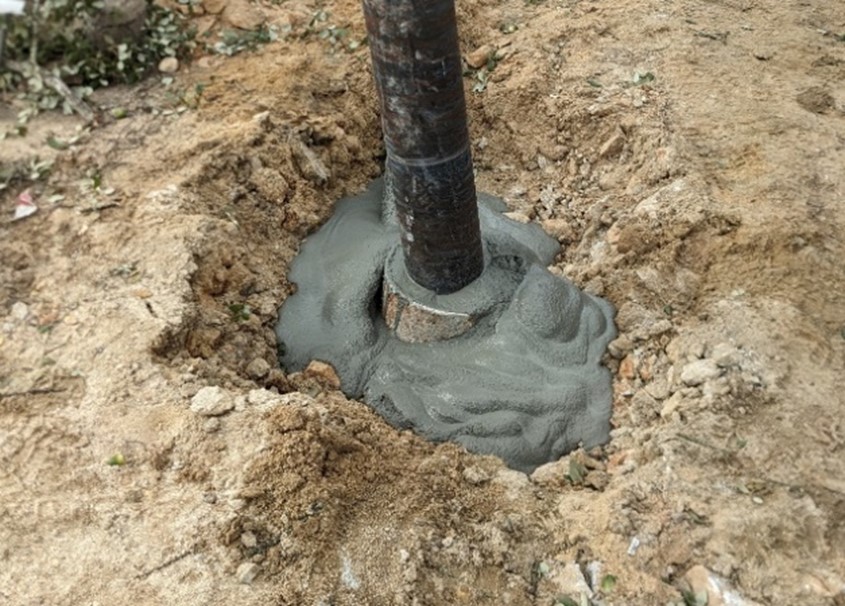
Solution
Shaft-grouted Ductile Iron driven Piles was the selected option to stabilize the earth dam. It is an effective solution to consolidate non cohesive soils and provide deep foundation to civil engineering structures. Micropiles are cost effective and can be installed in a relatively speedy manner. The shaft grouted option offers, in this particular case, better soil consolidation and improves skin friction.
GEO/ARCOS partnership was capable of providing the technical knowledge and skills to install the piles a per project specifications, all of them reaching depths where refusal was observed. The bearing capacity was proven by a static load test preformed onsite, with two loading cycles: up to design load of 326kN (100%) and to 651kN (200%).
Work schedule and concrete supply was carefully programmed, to avoid interruptions and optimize pile installation. Even having many no programmed stops, it was possible to complete all working micropiles (126 units) in one month.
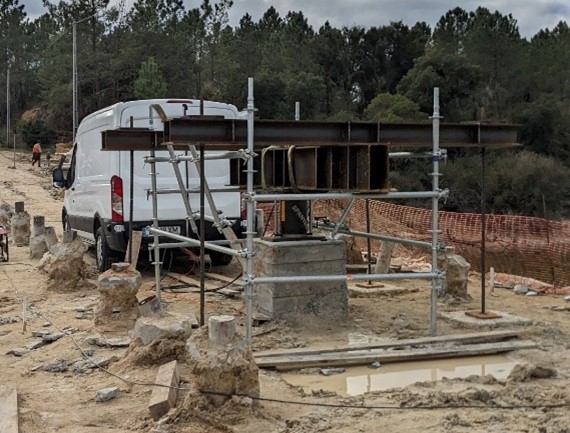

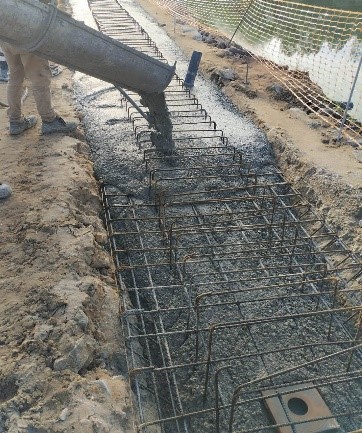
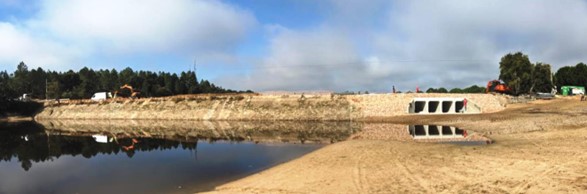
Key Figures
Scope:
A total of 126 Shaft-grouted Ductile Iron Piles: 88 vertical and 38 inclined (25°). These were all of 170/7,5mm and having a 270mm conical pile Shoe.
One vertical test pile and 4 reaction piles.
Achievements:
Maximum production of 14piles/day (170m/day) and average of 10piles/day. Efficient use of pipe with less than 2% wastage. Load bearing capacity proven onsite up to 651kN (200%) with <5mm of residual settlement.
Soil Conditions:
The site soil profile is basically composed by the earth dam, of silty sand soil (NSPT 2-5), from 0 to 9m depth, followed by ≈3m of alluvium silty, partially clayey, Sand (NSPT 9), with dispersed gravel, and a base of compact silty Sand (NSPT 48-60) at an average depth of 12m.